PET is a milky white or light yellow highly crystalline polymer with a smooth and shiny surface. It has good creep resistance, fatigue resistance, abrasion resistance and dimensional stability, low wear and high hardness, and has the greatest toughness among thermoplastics: good electrical insulation performance, small temperature influence, but poor corona resistance. Non-toxic, weather resistant, chemical resistant, low water absorption, resistant to weak acids and organic solvents, but not resistant to hot water immersion and alkali.
The glass transition temperature of PET resin is high, the crystallization speed is slow, the molding cycle is long, the molding cycle is long, the molding shrinkage rate is large, the dimensional stability is poor, the crystallization molding is brittle, and the heat resistance is low. Through the improvement of nucleating agent, crystallizing agent and glass fiber reinforcement, PET has the following characteristics in addition to the properties of PBT.
1. The heat distortion temperature and long-term use temperature are the highest among thermoplastic general engineering plastics
2. Because of its high heat resistance, reinforced PET is immersed in a solder bath at 250°C for 10S, hardly deformed or discolored, especially suitable for the preparation of electronic and electrical parts for soldering:
3. The bending strength is 200MPa, the elastic modulus is 4000MPa, the creep resistance and fatigue resistance are also very good, the surface hardness is high, and the mechanical properties are similar to those of thermosetting plastics.
4. Since the price of ethylene glycol used in the production of PET is almost half cheaper than that of butanediol used in the production of PBT, PET resin and reinforced PET are the lowest in engineering plastics and have high cost performance.
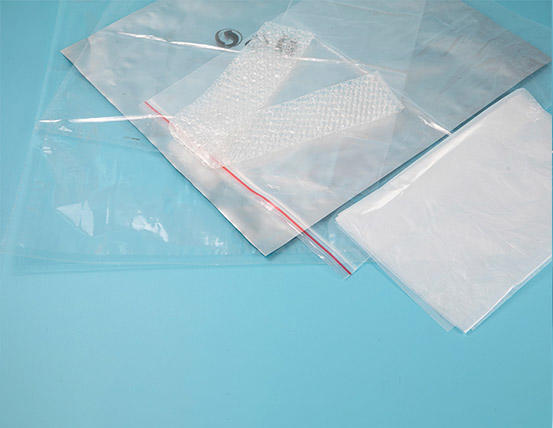
Second, pet protective film - molding of pet:
The molding process of PET can be injection molding, extrusion, blow molding, coating, bonding, machining, electroplating, vacuum metallization, and printing. The following mainly introduces two kinds.
1. Injection molding grade ①Temperature setting: nozzle: 280~295℃, front section 270~275℃, middle forging 265~275℃, rear section 250-270℃; screw speed 50~100rpm, mold temperature 30~85℃ , The amorphous mold should be below 70℃ and the back pressure should be 5-15KG. ②Try out the dehumidifying dryer, the temperature of the material tube is 240~280℃, the injection pressure is 500~1400℃, the injection molding temperature is 260~280℃, the drying temperature is 120~140℃, and the time is 2~5 hours.
2. At the film level, the PET resin slices are pre-dried to prevent hydrolysis, and then the amorphous thick slices are extruded through a T-die in an extruder at 280°C, and then quenched by a cooling drum or cooling liquid to keep them in place. Amorphous for stretch orientation. The thick sheet is then biaxially stretched by a tenter to become a PET film. Longitudinal stretching is to preheat the thick sheet to 86~87 °C, and stretch it about 3 times along the plane extending direction of the thick sheet at this temperature, so that the orientation can improve the crystallinity and reach a higher temperature: transverse stretching preheating temperature 98~100℃, stretching temperature 100~120℃, stretching ratio 2.5~4.0, heat setting temperature 230~240℃. The longitudinally and laterally stretched film also needs to be heat-set to eliminate the film deformation caused by stretching and make a film with better thermal stability.